So what in the world have we done so far? | The EIHS InvenTeam's Progress, December Edition
Hi there! Our project revolves around a type of additive manufacturing called fused deposition modeling 3D printing. If you’re unfamiliar with 3D printing, never fear, we’ve created a slide set with a bunch of relevant information about the manufacturing technique that can be found here. Now, on to the blog!
~~~~~~~~~~~~~~~~~~~~~~~~~
The Energy Institute High School, as a general rule, is a cool school.
We are biased, you might object, but your objections are futile.
Despite the coolness of our school, we identified a significant problem on-campus involving one of the most noteworthy manufacturing technologies of the 21st century--3D printing--that we believed needed solving.
In 2018, the Energy Institute High School purchased around twenty FDM 3D printers to be used for school projects, by our robotics teams, or for other miscellaneous endeavours. However, very few failed prototypes, brims/skirts, or support material on campus are recycled in an environmentally conscious way: they are usually discarded as waste or stored indefinitely. Consequently, Energy Institute has significant room for improvement with regard to PLA waste, as we currently do not have an easy way to recycle the plastic.
For more concrete evidence of the issue of wasted filament on campus, we interviewed Jessica Merino and Jordan Campbell, both engineering teachers at EIHS. Both teachers were in agreement about how frequently the 3D printers were used, but stated that there is currently not a streamlined way to recycle PLA products on campus. And looking at the issue from a financial standpoint, Ms. Campbell informed us that it was actually cheaper for the school to discard filament waste and purchase new filament, rather than recycle it manually.
After the virtual interviews and the recognition of our school’s filament recycling problem, the team settled on our driving question: how can we design a novel machine that increases filament recycling rates on campus?
We are the Energy Institute High School InvenTeam. These monthly blogs will document the planning, testing, and results associated with our attempt to create our product: a machine that will facilitate the reuse of wasted and discarded PLA filament by streamlining the re-printing process of the material with FDM 3D printers. Quite a mouthful.
Pre-everything tasks
Our team managers (Diya Patel, Oscar Davenport, and Ben Barnes; the original 3 team members) recognized that working remotely with a group of 10+ student peers would be an arduous task, and the issues that could arise multitudinous. They therefore attempted to mitigate the effects of these potential issues by planning out exactly how the team would be structured so that the full team could continue to function properly, no matter what curveballs the universe flung our way.
What we’ve accomplished
Last month, we had a total of 4 full team meetings (one meeting weekly), and, during these, made substantial progress. Below is a description of what each subteam accomplished during the month of November.
The Administration Team (Ben Barnes, Oscar Davenport, Diya Patel)
The administration team (A-team) manages team organization and workflow. A-team’s primary success last month was the creation of a comprehensive, consolidated team schedule using google sheets. A-team also delegated tasks to our team members during each meeting, and oversaw the smooth integration of any last-minute additions to our team.
The Communication Team (Oscar Davenport, Diya Patel)
The communication team (C-team) manages inter-team and team-to-Lemelson-MIT communication, local outreach, and our social media pages. Last month, C-team created our Instagram account (@eihs.inventeam; go follow us!) and ensured that all team members stayed in the loop about our team’s progress. Most significantly, C-team created a google spreadsheet with the contact information of local companies, which we will contact to ask about their willingness to support our team.
The Financial Team (Noah Hight, Diya Patel)
The financial team (F-team) manages all of the purchases and fundraising endeavours associated with our project. F-team created a google form for the Sustainability + Technical Teams, through which parts and materials could be requested and purchases for our final product made. They also brainstormed some ways that our team could fundraise (more on that next time!).
The Sustainability + Technical Teams (Orian Caldwell, Risto Djishev, Bella Johnston, Allie Kirchen, Cole Ledman, Ian McDaniel, Kendall Tauser)
Brace yourself; technical language is coming.
The sustainability + technical team (S+T) manages the actual design and assembly of our product. S+T’s tasks include the design (both mechanical and electrical), integration, manufacturing, and assembly of our machine.
This month, S+T’s huge success was settling on a way to achieve our goal of reintroducing scrap PLA back into FDM 3D printers. Though the schematic, shown in the infographic below, is similar to our team’s project proposal from our original InvenTeam application, we have modified parts of the design.
First, a filament shredding mechanism (similar in design, but not utility, to a paper shredder) will be mounted on one side of the 3D printer. Second, some sort of conveying system (belt, archimedean screw, vacuum pump, fan, etc) will direct shredded PLA material (called ‘pellets’) to a pellet hopper, mounted on the 3D printer’s crossbar. Below the hopper, a flexible (possibly collapsible) tubing will direct the pellets via gravity to our final step--a custom pellet extruder and hotend, engineered for compatibility with our school’s Ender 3 Pro 3D printers, which will collect the pellets from the shredder and extrude them directly onto the 3D printing build plate.
Since stage 1 of our machine will involve ‘busting’ filament, we decided to christen it the Filabuster.
During our second meeting, Orian Caldwell (one of our certified CAD wizards) showed the team his CAD draft of a pellet extruder design. As you can see, our pellet extruder will likely use a stepper motor mounted to an on-axis auger, and most housing components will likely be 3D printed with a heat-resistant material like PET-G (a variation of Polyethylene Terephthalate, whatever that means).
In our third meeting, Risto Djishev and Cole Ledman (other CAD wizards) showed us their concept for an archimedean screw design that would convey pellets from the grinding mechanism to the pellet hopper. Their design would eliminate the risk of pellets clogging the mechanism, since ideally the screw diameter could be quite wide. It’s worth mentioning that, with few adaptations, this screw conveying mechanism could be modified to work in space. Pretty neat.
The Research Team (Ben Barnes, Bella Johnston, Allie Kirchen, Diya Patel)
The research team (R-team) manages the blogs, our notebook, and our team website. Last month, R-team purchased/updated our team notebook, began the design of our website (again, more on that in the next blog), created some graphics/logo designs for our team (like the infographic above!), and wrote this blog, for the sole purpose of informing you, dear reader, of our team’s progress.
~~~~~~~~~~~~~~~~~~~~~~~~~~~~~~~~~~~~~~~~
Whew.
Effectively and accurately documenting our engineering process takes a lot of time, and we’re so grateful for the support we’ve received so far from people like you.
Again, feel free to follow our Instagram page @eihs.inventeam, or shoot us an email at eihs.ivt@gmail.com if you have questions or are a business/company who’d like to sponsor our project!
Have a great day,
-allie, oscar, bella, orian, kendall, ian, noah, cole, diya, risto, ben
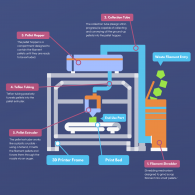