April Updates
Based on the feedback given to each Technical Team at our Mid Grant Technical Review, we have made significant progress on improving our next prototype. Below, each team describes the progress they have made in building their second prototype:
Materials Team
One of the most critical decisions made due to our feedback and test plans was selecting the material that would be used in the final prototype. Of the two materials used on our first prototype, 420 Denier Cloth and WeatherMax, we decided that Weathermax would suit our needs best due to its water repellency, insulating qualities, and durability. According to the design specifications, WeatherMax is a 100% solution dyed polyester that incorporates UV resistant characteristics for long-term color and strength retention along with excellent breathablity and abrasion resistance. The HydroMAX finish of the material is water repellent, mildew and oil resistant, has anti-microbial properties and a minimum UV resistance of 1000 hours but only weighs 6.5 oz./sq. yard due to the use of a filament rather than a spun yarn like acrylic fabrics.
In addition to these qualitites, we perfected our methods when it came to sewing the tent. We did extensive amounts of research as to which stitches would be best fitted for our purpose. We followed the guidance that was found in this research, as well as tweaked a few minor sewing errors we encountered through the process of making our first prototype. Most importantly, we’ve taken various precautions to ensure little to no mistakes are made while sewing, giving us a smoother process and better quality stitching.
In short, we took into consideration the various problem areas we found and worked on improving them to make sure we have maximum durability and functionality in our final tent.
Solar Power Team
At MGTR, the Solar team had the codes for the PIR sensor and LED light and countdown timer working separately. Since then we’ve integrated the code for the PIR sensor, UV-C (blue LEDs we’re using in place of actual UV-C LED lights), and countdown timer. With regards to the countdown timer, we have stopped using it and are now working on integrating our code for the LCD display and PIR sensor and UV-C lights. As previously mentioned, our team was only using a single LED light with our PIR sensor at MGTR, but we have since soldered white LED lights and blue LED lights (acting as our UV-C lights) onto separate stripboards to accommodate the design we have come up with for our final prototype. Moreover, we decided that we needed a case to house all the wires, battery, Arduinos, USB ports, push button, sensor, and lights.
We are currently started a 3D design for our case because our team will 3D print it. Additionally, our team is also working on integrating our PIR sensor and UV-C lights code with our LCD display code to get them to work together. We are also working on connecting our white LED lights to a switch so that the user is able to get light whenever they need it and to not risk them confusing the UV-C light button and regular white LEDs and turning on the UV-C instead because that is very perilous. More recently, we ordered a logic level and got it to make our LEDs brighter because the Arduino would take all the power and leave our lights very dim.
Structures Team
Since our Mid Grant Technical Review, Structure’s team has applied itself to ameliorate our first prototype. One of our first steps was to make decision on what would happen to the fiberglass rods we were using for our first prototype. As a team, we came to the conclusion that we had two options for the fiberglass poles, we either cut the poles to a shorter length or we can leave the poles that we currently had. We decided that we would keep the current fiberglass poles, 13 feet with a ¼ diameter, to facilitate the process of developing our final prototype. We also had to make a decision on the tent clips that are used at the bottom of the fiberglass rods. We then came to conclusion that instead of developing new clips, we should just add a safety feature to the tent in general so that it can be safer for the occupants to open.
The next step we took was breaking into two smaller groups in order to complete the goals that we had set. Two members from our team worked on refining the backpack for the tent. First we drew out an outline of what the backpack would look like and then they worked on cutting the material. Right after this process, they started sewing it together and they also added the rolling capability, which was one of the requirements for our backpack. The other 2 person group worked on enhancing the lap table, which was an added feature to our tent. The first step we took was deciding what materials we would be using, including the base and the material to cover it. We then worked on sewing polyester onto the base and adding velcro onto it since the lap table will be attached onto a part of the tent. Furthermore, we also added a plastic mirror sheet, which was a feature that we agreed our lap table should include.
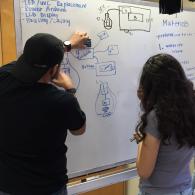